What You Need To Be Aware Of About The Press Brake
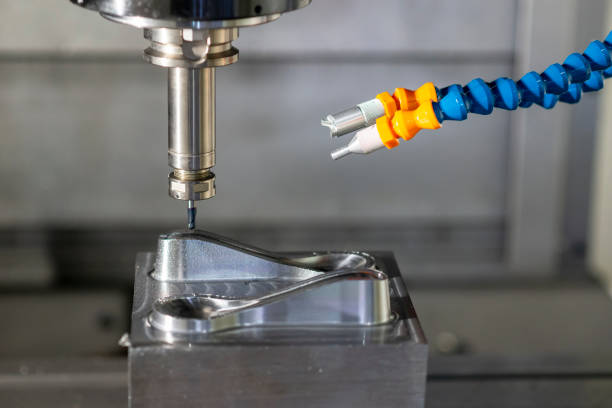
The sheet is typically bent by one stroke of an drum. By changing the press
brake's dies and bending the sheet several times, it is possible to create more
complex cross-sectional designs. In the forging process, the CNC press
brake manufacturers" is now one of the most popular metal forming
equipment.
It is widely utilized in shipbuilding, aviation railways, electrical
engineering, mining and engineering machinery, metallurgy automobile,
agricultural machinery, instruments, light industry, textile, electronics and
other industries.
People have increased demands for premium materials due to the advancement of
humanity and continuous improvement in production and productivity. The industry
of people's livelihood are in need of the high-precision bender like high-speed
rails, electric power, elevator, decoration, manufacturing of machinery
kitchenware, anti-theft etc.
Classification of press brake machine
This is the most popular model currently available. A majority CNC press
brake machine manufacturers use this design.
The press brake's primary technology is the synchronous control accuracy. It
has a direct impact on the performance and the quality of the component.
Based on the different control techniques employed by the ram, the ram can be
divided into the following:
Torsion shaft synchronous brake machine
Machine for hydraulic press synchronous
Electro hydraulic proportional technology
In the latter part of the Second World War, the speed of jet fighters is
continuously increasing, and the control system is now having greater demands on
speed as well as dynamic accuracy and rate.
The plane's first electro-hydraulic system was introduced at the end of
1940.
In the 1960s, all types of electro-hydraulic servo valves came out and
electro-hydraulic-servo technology became increasingly advanced.
The demand for electrohydraulic technology in civil engineering increased
rapidly and extensively during the 1960s. However, the standard
electro-hydraulic valve has extremely specific requirements for fluid medium,
and the system energy consumption is also significant, meaning that the cost of
manufacturing and maintenance are extremely high, which makes it difficult to
accept by industrial users.
Electro-hydraulic proportional control was developed quickly in the 1970s to
provide an electro-hydraulic technology for control that could meet the needs of
engineers in the field.
In the same period, industrial servo control technology was also
developed.
The electro-hydraulic proportional technique is a fully-integrated technology
that not only realizes hydraulic power transmission but permits precision and
flexibility to be controlled electronically.
The growth of numerical control technology and the creation of reliable proportional hydraulic components have made electro-hydraulic proportional technology a common tool in recent years. An example is one used to synchronize the brake press.
Comments
Post a Comment